![]() |
Is there any simple way to control the health of the coverage of Welding Electrodes? |
![]() |
From superficial view welding electrode shall have a smooth
surface without any kinds of crack, colorless without any
holes and extra materials on it. All of above can be
observed by eyes without any instruments. |
![]() |
What is the importance of Ampere in welding the Electrodes and what is the base of choosing the appropriate Ampere? |
![]() |
Usually we adjust the current of Electricity base upon the
Diameter of Welding Electrode.
With the bigger diameter we need to increase the
current of Electricity. Always we should follow the
manufacturer instructions about the current of Electricity
but if there is no Ampere table available we can refer to a
general rule: the Ampere has a relationship of one
thousandth inch with the diameter of welding electrode.for
example if the diameter of electrode is 3.25 mm ,this is
equal 0.125 inch so we need 125 amperes for welding this
electrode.
Below are some disadvantages of welding spot if we do not
consider the above instructions:
A-
If we use the lower Ampere of the normal range: The welding process
becomes difficult and we can’t have a smooth surface of
welding.
B-
If we use the upper Ampere of the normal range:
1-
The second coated part of Electrode will burn soon and it won’t
have the suitable situation for welding.
2-
High Spatter.
3-
Slag becomes more adhesive (remove of slag becomes very
bad)
4-
Weld metal doesn’t have a suitable surface so
the strength of the weld metal decreases.
5-
The Mn of weld metal will burn and it can
break easily.
6-
It sound the smoth of Welding is increasing.
Some Welders use the high Ampere to weld easier but they
forget the above problems. |
![]() |
Is pre-heating necessary for Welding electrode? How we can understand it is necessary to pre-heat a welding electrode? |
![]() |
It is not necessary to pre-heat electrodes except
low hydrogen
ones or if
electrode absorbed humidity before.
It is not easy to understand if the electrode absorbed
humidity but one of the signs is the saltpeter on the coatig
of it or high spatter during welding.
If the spatter during a unique welding electrode varies it
shows the electrode
has absorbed humidity , in this way the slag would
differ as well in two parts of the same electrode.
If an electrode has absorbed humidity it is recommended to
do pre-heat. |
![]() |
What are the reasons of cracking in weld metal and how can avoid the crack in welds? |
![]() |
There are some reasons which make crack during of welding or
after welding as below:
1-
Nonconformity of the analysis of base metal with welding electrode.
2-
Nonconformity of dimension of base metal with type and size of
welding electrode.
3-
Usage of Inappropriate
current in welding
4-
Unskillful welding to
shape a smooth welding spot
5-
Situation of welding impurity of base metal effect the
welding and cause a loose strength.
6-
Welding in a bad condition: Welding in rainy, cold and windy
weather may cause the quality of welding spot as well as
ignoring the basic elements such as pre-heating.
7-
Usage of low quality electrodes ( wet electrodes and electrodes
with inappropriate chemical analysis) |
![]() |
When do we need to pre-heat the base metal? |
![]() |
Pre-heat cause the decrease of the speed of the cooling in
the weld spot and the affected surrounding by the welding.
There are some parameters to appoint the temperature of the
base metal such as dimension of the base metal , the
analysis ,strength and diffusible hydrogen of weld metal. |
![]() |
How do we distinguish the expiry date of the welding electrodes? |
![]() |
If we follow the suitable storage methods so the electrode doesn’t absorb any humidity we can use it after a long while otherwise the only issue which can cause low quality of weld is the humidity absorbed by the coating of electrode. |
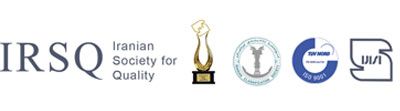